
BLOG 11 - Manage The Project
...Not the Plan
05-03-16
Test
One of the most pertinent reflections from the project was the size of the task of testing components and the importance of doing this as early as possible. Some delays were caused by parts not performing to their expected level which could have been identified sooner had more rigorous testing been carried out. For example, when one of two similar products began to experience a drop in performance they weren’t immediately directly compared to determine the issue. As the productive was defective it was replaced by the supplier at no extra cost but the delay in a replacement being dispatched meant there were 3 days in which the car could not run. A third part could have been purchased as a spare and swapped in in the event of a failure but this would have added extra expense to the project so more thorough testing as an earlier stage would have resulted in the delay occurring sooner and posing less risk to the project.
Buy or manufacture?
A compromise had to be struck between manufacturing parts ourselves (generally cheaper) or buying products off the shelf (likely to result in higher quality). Since a significant reason for constructing the chassis from aluminium was that it was donated by a local supplier, this freed up more budget to purchase off-the-shelf parts where quality was considered a high priority. This was mainly the rear axle assembly where the bearings had to run smoothly and the coupling strong to hole the axle to the motor while potentially spinning at speeds in excess of 700rpm. Because this was considered a key constituent of the drivetrain the risk of manufacturing low quality parts which may induce too much friction or increase the likelihood of failure was one that was worth the extra expense to mitigate. The front axle was not considered strategically significant so was manufactured in-house.
Communicate clearly!
One of the most helpful practices of regular meetings was the task review at the end of every meeting so that everyone was aware of their own, and others’, responsibilities for the coming week. This is supported as a good practice for keeping team member expectations in check by the project management website teamgantt.com.

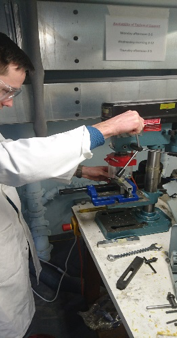

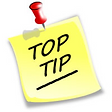
Top tip!
Regardless of the issue arising, whether it was significant or had little bearing on the project it was important that the team reacted to it in a way that best ensued successful completion of the objectives and managed the project and not the plan. Forcing the project to meet the original plan would have been naïve and allowed delays and complications to hinder the project instead of mitigating their impact. Although important to determine the cause of the problem, spending too much time apportioning blame would give less time to finding a solution.
“Lists always help to track tasks, milestones, and related deliverables. When your whole team has access, there’s never a question about who is doing what and when to expect task completion.”